good idea getting a seperate grinder, although my workshop is now absolutely crammed full.
I bought one of these, only 3" wheels so pretty compact. The flexible extension has come in handy as well.
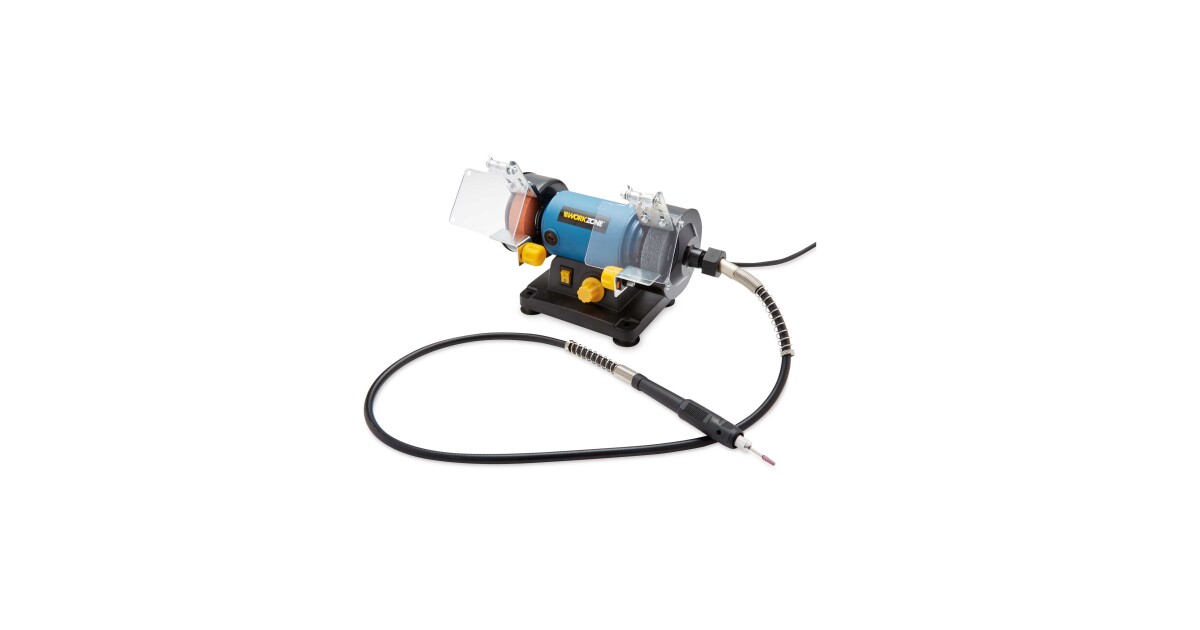
good idea getting a seperate grinder, although my workshop is now absolutely crammed full.
I'll have a wonder tomorrowI bought one of these, only 3" wheels so pretty compact. The flexible extension has come in handy as well.
![]()
What are you exactly doing there with the door cards?![]()
What a cute fuselage you have thereWhat is the year of construction and engine displacement and chassis type for your Peugeot?
Nice to learn that a 1.6 engine didn't look it up but not very fast (sorry) can have such a fuselage. I am attempting to find the overbuild factor for our Nissans and from Toyota I am aware that the 80 - 90 cars where 150% - 200%. And for your fuselage and for example 1.2 gearboxes I saw opened up and at the engine but then just hanging there, no cabling and stuff, I believe it is very neatly done but then I wonder what overbuild factor is there. Just to learn how much HP it can take. I think my CG13DE gearbox can take 112 tot 150 hp and still be as reliable as intended but hoping to find out by racers hearts how much it really is. And for that, how much it is on very new cars like 2003. For me that is quite new![]()
my cg13 box withstood 163hp for few years easily, but very dependent on driving style, whether it's abused on drag strip or sustained trackdays or just driven on the street.
I would have thought that hacking those front strut top mount turrets is an instant MOT failure! Looks to have really compromised the strength of the formed turret topJamie from LetsTorqueCars fitted new coilovers on his bmw but said the rear was extremely stiff & bouncy
View attachment 73292View attachment 73293
surprised to see he chopped bits off the turret to clear the camber adjuster
I noted that he could've just rearranged the allen screws without cutting it, plus you can see the camber ain't set equally
View attachment 73294View attachment 73295View attachment 73296
the rear damper was actually set too short which was pre-compressing the spring till it's rock solid so I reconfigured the bumpstop and lengthened the damper.
View attachment 73297
turns out the supplied springs of 7-8kg/mm front/rear were wayy too stiff and high so I suggested he looks for a softer 4-5kg/mm set to lower the ride height and bring the damper travel within better range.
I would have thought that hacking those front strut top mount turrets is an instant MOT failure! Looks to have really compromised the strength of the formed turret top![]()
Nice work on the cart, how's the TIG welding coming along?
Re your undoing hub nuts, I had this with our rally car. I now use Nissan Note 1.4 hub nuts which fit fine and are Nyloc as standard. That plus a load of threadlock keeps them in place. I then use the split pin as a marker with a dab of red paint on the nut to show any movement.
It might be worth giving it a wash, use a scrubbing brush and a bucket of warm soapy water and a clip to hold the seat belt out / stop it retracting and scrub away, often they are stiff because of the gunk in the webbing making it less flexible and harder to retract.* passenger seat belt struggling to retract - always had that issue but I'll soon be replacing these old units with the modded 3dr facelift belts.
The belt looks fine and still flexible. It's probably the spiral spring mechanism which has weakened and sticking.It might be worth giving it a wash, use a scrubbing brush and a bucket of warm soapy water and a clip to hold the seat belt out / stop it retracting and scrub away, often they are stiff because of the gunk in the webbing making it less flexible and harder to retract.
Cheers I'll order someNissan Note 1.4 hub nut with Nyloc is what you need....
I used Audi rear caliper seals on my 22v spare set lol , loads share basic sizes ,the 54mm is a odd one lol
And maybe using Suzuki vitara pistons, kr those were the same at the time ,
And found a reference in could use Audi slide pins
So always worth a cross ref at times tbh
Still need to machine the carriers to fit k11 pins
Sent from my LM-Q630 using Micra Sports Club mobile app