wehey
Ex. Club Member
hiya all
I have just attempted my first bit of welding and would appreciate a bit of advice.
There is a ton of welding to do on the Pao so I decided to make a start in the wheel well before trying exterior bodywork, as its hidden and won't matter as much as it not often seen.
I brought some 0.8mm m/s sheet and did a load of practicing, playing around with the various settings until I managed something the resembled a weld.
Below is a pic of the result of my first patch and although it does the job its a right bloody mess and definitely needs to improve before tacking bodywork
Can anyone tell from the pic if the mig is set up correctly. I.e can any heat, wire speed and gas setting be tweaked to get a better result. All criticisms kindly received
No laughing now.....here's the pic
I have just attempted my first bit of welding and would appreciate a bit of advice.
There is a ton of welding to do on the Pao so I decided to make a start in the wheel well before trying exterior bodywork, as its hidden and won't matter as much as it not often seen.
I brought some 0.8mm m/s sheet and did a load of practicing, playing around with the various settings until I managed something the resembled a weld.
Below is a pic of the result of my first patch and although it does the job its a right bloody mess and definitely needs to improve before tacking bodywork
Can anyone tell from the pic if the mig is set up correctly. I.e can any heat, wire speed and gas setting be tweaked to get a better result. All criticisms kindly received
No laughing now.....here's the pic
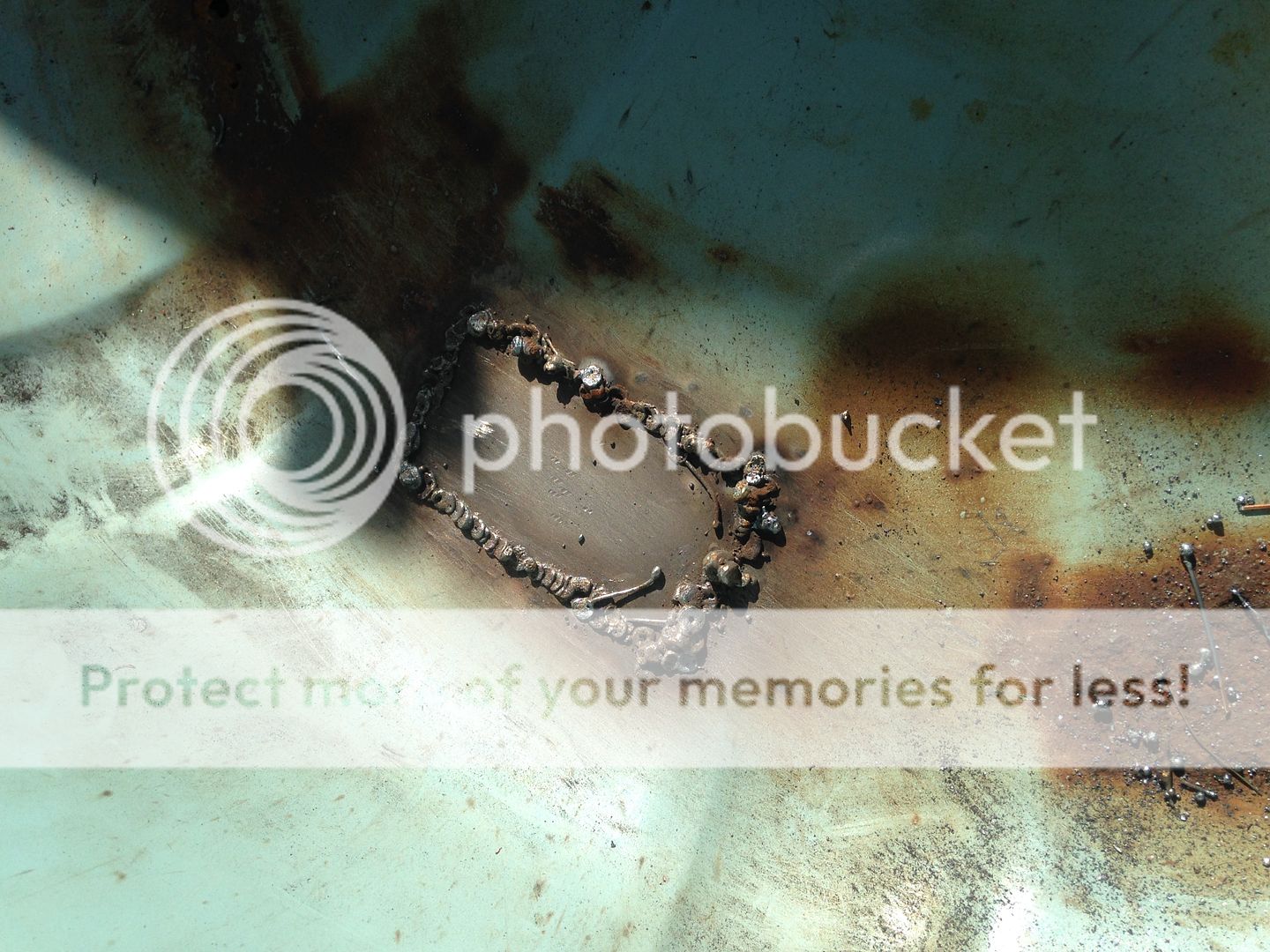